Plate Heat Exchangers
- Home
- Industries
- Plate Heat Exchangers
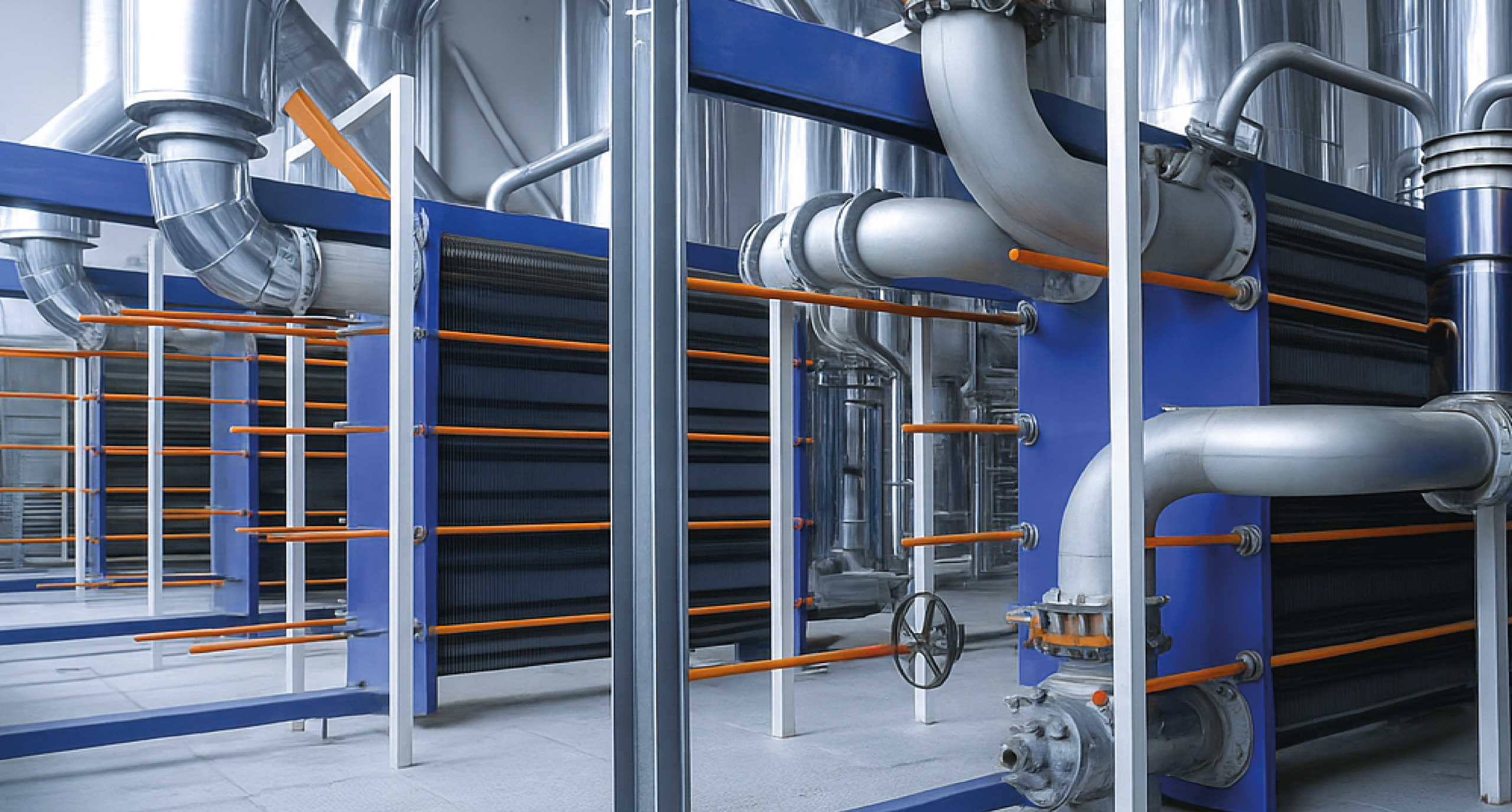
Plate Heat Exchangers
Maximizing Efficiency: The Power of Plate Heat Exchangers Across Industries
Dolphin Plate Heat Exchangers are designed to deliver energy-efficient thermal transfer across a wide range of industries and systems. With decades of manufacturing experience and a global footprint, Dolphin brings together engineering excellence, material science, and certified performance to serve complex cooling and heating requirements.
We offer a full range of PHE configurations:
- Gasketed Plate Heat Exchangers (GPHE)
- Semi-Welded Plate Heat Exchangers
- Brazed Plate Heat Exchangers (BPHE)
Each product is engineered to meet international performance benchmarks and designed to minimize energy consumption, reduce footprint, and ease maintenance.
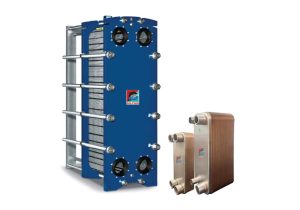
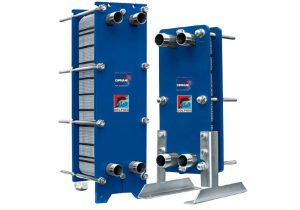
Features and Benefits
- High Thermal Efficiency: Provides excellent heat transfer performance due to large surface area and turbulent flow across plates.
- Compact Design: Offers a space-saving solution with higher heat transfer rates compared to traditional shell-and-tube exchangers.
- Ease of Maintenance: Plates can be disassembled for cleaning, inspection, or replacement, reducing downtime.
- Flexible and Scalable: Can be easily expanded or adjusted by adding or removing plates to meet changing process requirements.
- Low Fluid Volume: Requires less fluid to operate, which leads to quicker temperature control and energy savings.
- Wide Range of Applications: Suitable for both heating and cooling processes in industries like chemical, pharmaceutical, food processing, refrigeration, and HVAC.
- Wide Range of Applications: Suitable for both heating and cooling processes in industries like chemical, pharmaceutical, food processing, refrigeration, and HVAC.
- Material Versatility: Available in stainless steel, titanium, and other alloys to handle various corrosive or high-temperature fluids.
Global Certifications
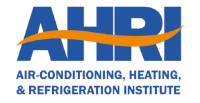
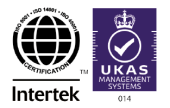
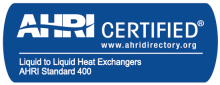
Gasketed Plate Heat Exchangers (GPHEs) are designed for efficient heat transfer through a configuration of corrugated metal plates sealed with high-performance gaskets. This design keeps hot and cold fluids in separate flow channels, ensuring effective thermal exchange while preventing cross-contamination.
The modular plate design enhances heat transfer surface area and enables easy maintenance or capacity upgrades. GPHEs are compact, adaptable, and well-suited for applications across multiple industries including HVAC, power generation, refrigeration, food processing, and chemical processing.
Key Features
- Ideal for applications requiring frequent cleaning or maintenance
- Plates can be easily added or removed for capacity adjustments
- Suitable for moderate pressure and temperature conditions
- Common in HVAC, food & beverage, and general industrial processes
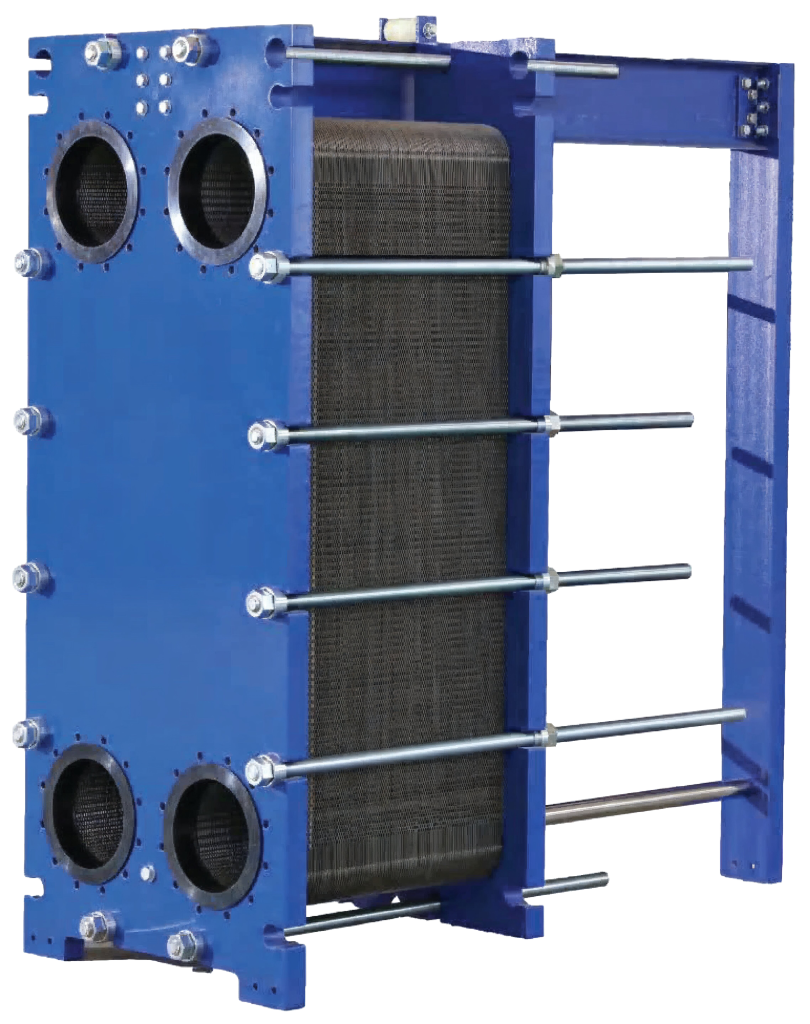
Plate Materials
304/304L, 316/316L, 254SMO, Titanium, Hastelloy C-276, Nickel and other options available
Gasketed Materials
EPDM, NBR, HNBR, Viton, CR and others available Max Design Pressure: 30 bar Max Design Temperature: 200°C
Dolphin Brazed Plate Heat Exchangers are fully sealed, maintenance-free units ideal for compact thermal systems. Built with stainless steel plates and brazed using copper or nickel, they are perfect for HVAC, refrigeration, and energy recovery applications.
Key Features
- Highly efficient and compact design
- No gaskets, making them suitable for high-pressure and high-temperature use
- Maintenance-free, but not serviceable
- Common in refrigeration, HVAC, and small-scale process heating
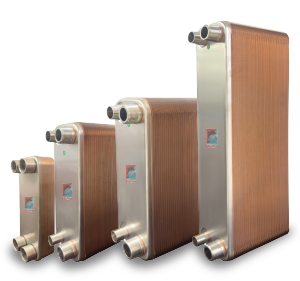
Available Variants
- Copper Brazed General HVAC, chillers, and hot water systems
- Nickel Brazed Corrosive environments or deionized water use
- Fusion Bonded Stainless Steel Extreme media and hygiene-critical operations
Semi-Welded Plate Heat Exchangers are engineered for demanding applications involving aggressive or hazardous fluids. Each exchanger consists of a pair of plates laser-welded on one side to form a sealed channel for corrosive media, while the other side uses gaskets for standard sealing.
This construction ensures reliability and safety under high pressure and temperature conditions, while minimizing leakage risk. Semi-welded PHEs are ideal for industries such as chemical processing, petrochemicals, oil and gas, offering high thermal performance with long operational life.
Key Features
- Suitable for corrosive or high-temperature environments
- Can handle higher pressures than gasketed or brazed designs
- Less maintenance, but limited accessibility for cleaning
- Often used in chemical, petrochemical, and power generation industries
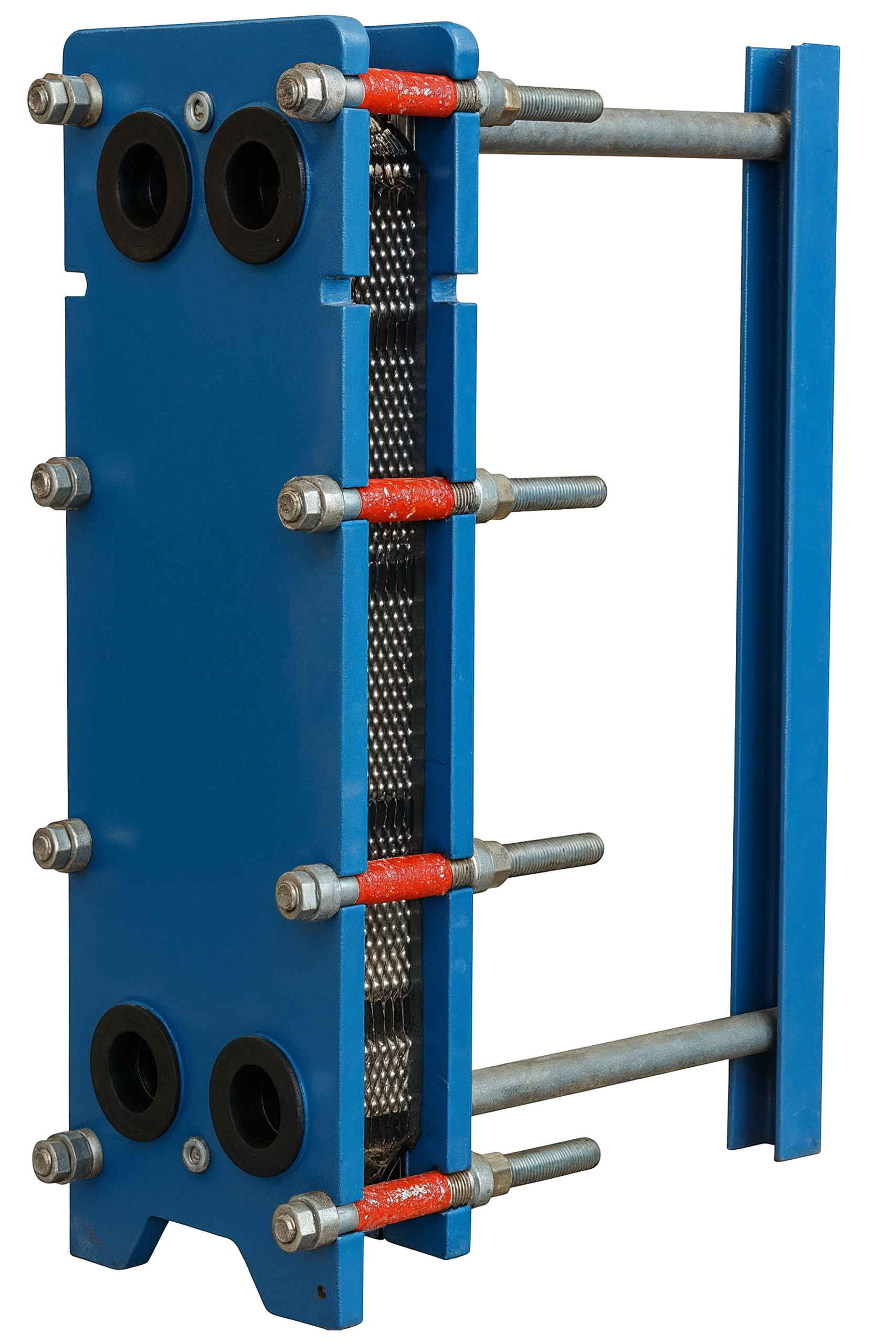